Customised container transformer station
Special performance requirements and conditions on site
A large plastics manufacturer asked for a container transformer station incl. a power supply to expand the connected load. Medium voltage switchgear (MSP plant), low voltage main distribution (LVM) and transformers with special requirements with us.
The total power of 4,000kVA was to be drawn from the internal supply network.
The particular challenge in the performance was the size of the station. For this could not be longer than 10m. Available standard 20-feet containers, 6.058m long, were too small to accommodate the required equipment and transformers. A 40-feet container with a length of 12.192m would have been too large for the conditions on site.
Due to the high performance requirements and conditions on site, we produced a container in special design together with our partner:
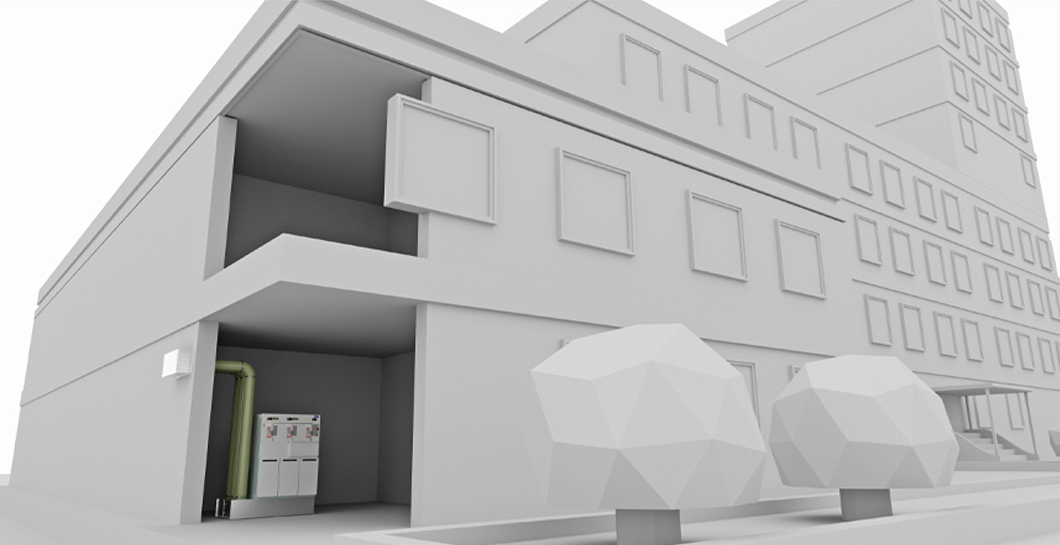
In order to be able to respond flexibly to our customer’s requirements, we planned the container to exact dimensions together with one of our container suppliers.
Two transformers of 2,000kVA each were installed in the special container, which was exactly 10m long. The switchgear room with medium-voltage switchgear system, low-voltage switchgear, accessories and components for connection to an existing fire alarm system was created between the transformer rooms.
Ihr Team von Horstmann & Schwarz